Definition of cold galvanizing
Cold galvanizing is also known as electrogalvanizing, and this kind of zinc-plated method is used for protecting metals from being corroded. We apply zinc fillers paint to the protective surfaces by any coating method, and the paint will form zinc layers after it dries, which contain up to 95% of zinc.
Cold galvanizing process is applied to a variety of steel products and anti-corrosion of structures.
Processing technique of cold galvanizing
(1)
Surface treatment of new steel
We need to choose mechanical derusting (sand blasting or shot blasting) before
cold galvanizing the new steel so as to make the surface cleanliness reach ISO 8501-1 Grade Sa 2.5, which is equivalent to GB 8923 Grade Sa 2.5.
Meanwhile, another quality indicator of surface treatment for cold
galvanized pipes is roughness.
Different cold galvanized materials have different requirements of roughness. In Zinga construction instructions, the average roughness is required to be Ra=12.5, namely, the Rz is between 55 and 75 microns; while in construction instructions of Roval, requirements of roughness are lower. That is, Rz is between 40 and 60.
If
cold galvanizing films are formed alone and are used for anticorrosive coatings, their surface roughness should be controlled to be slightly small to ensure the thickness of cold galvanized coating; when
cold galvanizing is used for bases of heavy-duty coatings, and the thickness of the coatings is over 180 microns, the surface roughness of the new steel should be greater than 60 microns so as to ensure adhesive forces of the whole coatings.
(2)
Surface treatment of the old steel
It is best to use sandblasting method to remove the old paint films and rusty stain so that the steel surfaces have a certain roughness. If the conditions are limited, we can also use grinding method by hands, pneumatic or electric tools to remove rust. This kind of method can reach ISO 8501-1 Grade St 3, which can remove the rust completely by hands and power tools. The literal definition is " There should not be visible grease and dirt on the surfaces and the surfaces should barely have oxides, rust, the old coatings and sundries. The surfaces should have metallic substrate gloss". Cold galvanized materials with different brands have different grades on surface treatment's requirements. For example, about five percent of slightly rusty area on the old steel's surface is allowed before Belgium Zinga coatings; when the steel's surfaces are polished by ROVAL and reach Grade st3, ROVAL coatings with 60 to 80 microns (thickness of dry films) have a good adhesive force for the steel. In the pull-off tests of the ROVAL coatings which are tested by China Shipbuilding Technology Research Institute, the adhesive force can reach 6.1MPa.
(3)
Surface treatment of welding seams
Welding seams are the most corrosive parts for steel members. It has been found that
cold galvanizing is an effective and economical method to patch the welding seams after we install steel members which are coated with the arc spraying zinc (aluminum) and hot-dip zinc by welding. We need to seriously remove "spatter", "welding slags", "welding fumes", grease, penetrant systems and other dirt, and then polish the surfaces to ISO 8501-1 Grade St 2 before patching the surfaces. After the surface treatment, we should immediately have the cold galvanizing of the surfaces for the first time.
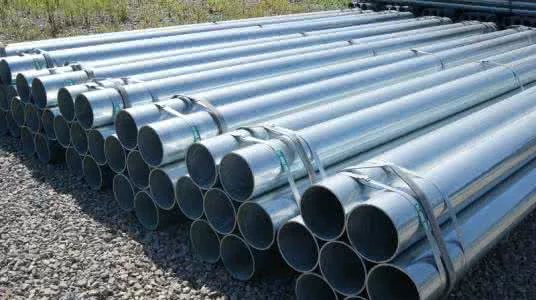