The appearance of the welding seam of the
steel pipes produced by the two welding torches was inspected, and it was found that the last 10 steel pipes produced by the traditional welding torch had the following problems compared with the steel pipes produced by the newly designed welding torch.
(1) Undercut of the welding seam
The continuously fed welding wire conducts the welding current through the contact tip. After a long time of use, the contact tip of the traditional welding torch causes the aperture of the contact tip to be bigger, which cannot clamp the welding wire. The contact tip loses the role of guiding the welding wire, and causes poor conductivity. The undercut occurs.
(2) Welding arc break
When using a traditional welding torch to weld, if the contact tip is not wear-resistant or high-temperature resistant, it will lead to poor contact after a period of use; heat and redness will appear, resulting in low conductivity efficiency. The contact area between the inner aperture and the welding wire is small. The conductive area is not enough. During large-scale welding, the contact tip and the welding wire will heat up, which will easily cause the welding wire to stick to the contact tip. During welding, spatter will stick to the tip and block the welding tip. This will cause the arc to stop. Replacing the contact tip will affect the operating efficiency of the unit and the first pass rate of the welding seam. The new welding torch can continuously cool down the contact tip through air cooling, effectively avoiding the above problems and reducing the frequency of stopping.
(3) Morphology of welding seams
In the production process of spiral seam submerged arc welded pipe, there will be uneven weld seam width, mainly because the conductivity of the traditional welding torch will change after the contact tip is worn, which directly affects the quality of the welding seam. In the welding process, the current and voltage vary greatly, resulting in uneven width of the welding seam.
The temperature at the end of the welding wire is too high, and the power voltage is reduced. Under the same welding voltage, the arc is elongated, and the penetration depth becomes shallow. Because of the intermittent contact of the worn contact tip, the depth of fusion is inconsistent, and incomplete penetration defects are prone to occur. After the depth of penetration becomes shallow, the deposited metal covers the surface of the welding seam, causing the weld seam reinforcement to be too high. The problem with the appearance of the welding seam is shown in Figure 8.
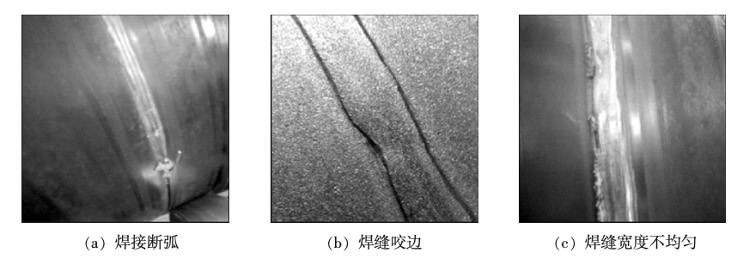
(a) Welding arc break (b) Welding undercut (c) Uneven width of the welding seam
Figure 8 The problem of the appearance of the welding seam
Analysis
(1) Welding deviation tests of internal and external welding seams
Through two sets of internal and external welding deviation tests, it was found that the first set of tests had little effect on the internal and external welding deviation due to the short use time of each welding torch and the contact tip was not worn; the second set of tests showed that the traditional contact tip wears seriously as the use time increases. The inner diameter increases or loses roundness, and the welding wire deviates from the position of the base metal seam, resulting in deviation of the inner and outer welding seams of the steel pipe. The contact tip of the newly designed welding torch adjusts the position of the welding wire according to the use time, which can effectively reduce the welding deviation caused by the deviation of the welding wire. However, it is necessary to summarize the method of adjusting the position and time of the newly designed welding torch and welding wire to avoid welding deviation caused by no adjustment.
(2) Impact tests
As the welding time increases with the traditional contact tip, the wear of the contact tip increases and the conductive area decreases, increasing in the temperature of the welding wire and a decrease in the penetration depth. To ensure penetration, it is necessary to increase the current and increase power consumption; the welding line energy increases, and the impact toughness of the welding seam decreases. The use of the new welding gun can effectively avoid the phenomenon of adjusting the current due to the wear of the conductive tip. At the same time, the temperature of the welding wire can be effectively reduced, ensuring the stability of the current and voltage in the welding process, the stability of the impact energy of the welding seam and reducing influence factors for analyzing engineering project data.
(3) The morphology of the welding seam
Because the contact tip of the traditional welding torch cannot be adjusted after it is worn out, the new design of the welding torch can prolong the use of the contact tip by adjusting the position of the welding wire, which ensures that the direction of the welding wire leaving the contact tip remains unchanged, and the output center of the welding wire does not change at all times. Problems with the appearance of welding seams and welding wire jamming caused by welding wire deviation can be avoided, ensuring stable conductivity of the contact tip, stable welding penetration, and good welding effect. At the same time, because the conductive connecting rod is equipped with a cooling air duct, the temperature of the conductive connecting rod and the contact tip can be cooled, thereby reducing the temperature of the welding wire, achieving the purpose of maximum penetration and low power consumption under the same welding specification.
Conclusion
(1) The newly designed submerged arc welding torch can always ensure that the welding wire is in contact with one side of the contact tip, and the position of the welding wire is stable during welding. The temperature of the welding wire can be effectively reduced by air cooling, and the welding seam morphology and physical and chemical properties are improved under the same working conditions.
(2) The currently designed welding torch structure has shortcomings. The device cannot be adjusted for multi-wire welding. At the same time, it is relatively easy to use the transmission mechanism to adjust when the diameter of the inner welding pipe is large, and the adjustment is not easy when the pipe diameter is small.