Temperature is the most critical environmental factor influencing CO₂ corrosion, as it affects the dissolution, precipitation, and composition of the corrosion product film, thereby altering the overall corrosion process. At low temperatures (≤60 °C), the dissolution rate of FeCO₃ exceeds its precipitation rate, preventing the formation of a protective corrosion product film unless the pH is increased. At higher temperatures (60–90 °C), the dissolution rate of FeCO₃ decreases, while its precipitation rate increases. This promotes stronger adhesion of FeCO₃ to the substrate surface, resulting in the formation of a more protective corrosion product film and a corresponding reduction in the uniform corrosion rate.
Moreover, temperature also influences the composition of the passivation film, which in turn affects the material’s corrosion resistance. Yue et al. reported that the passivation layer on super 13Cr at 90 °C primarily consists of amorphous Cr₂O₃ and a small amount of Cr(OH)₃. When the temperature rises to 200 °C, the transformation of CrO₃ into FeCrO₄ is promoted, providing additional pathways for ion transport. This increases the driving force for Fe ions to migrate from the inner interface to the outer surface, thereby accelerating the corrosion rate, as illustrated in Figure 18.
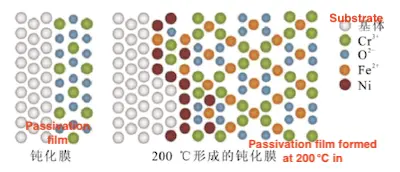
Figure 18 The composition and element migration of the passivation film on super 13Cr at 200 °C
In oil well engineering, the critical corrosion rate is commonly used as a benchmark for material selection. According to field service requirements, a threshold of 0.125 mm/a is typically adopted. The critical corrosion rate of martensitic stainless steel seamless pipes is influenced not only by CO₂ partial pressure, but also by temperature, pH, chloride ion (Cl⁻) concentration, hydrogen sulfide (H₂S) partial pressure, and other environmental factors.
To isolate the effect of CO₂ partial pressure, Kimura et al. investigated its influence, along with temperature, on the corrosion rate in a 20% NaCl solution saturated solely with CO₂. The results indicated that the uniform corrosion rates of both standard 13Cr and improved 13Cr steels increase proportionally with CO₂ partial pressure. Furthermore, as temperature increases, a lower CO₂ partial pressure is required to reach the critical corrosion rate, as shown in Figure 19.
- 13Cr, corrosion rate ≤ 0.125 mm/a
- 13Cr, corrosion rate > 0.125 mm/a
- Improved 13Cr, corrosion rate ≤ 0.125 mm/a
- Improved 13Cr, corrosion rate > 0.125 mm/a
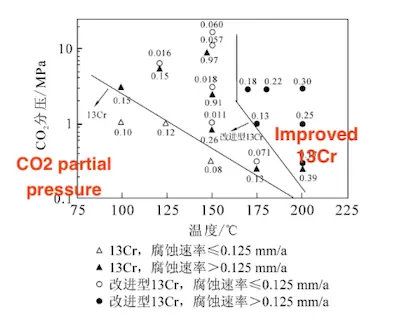
Figure 19: Effect of CO₂ Partial Pressure and Temperature on the Corrosion Rate of Martensitic Stainless Steel in a 20% NaCl Solution
Interestingly, the influence of CO₂ partial pressure on the corrosion of X65 carbon steel varies under different conditions. According to research by Sun et al., in the absence of a corrosion product film, the uniform corrosion rate increases with rising CO₂ partial pressure. However, once a complete protective film has formed, the corrosion rate becomes largely unaffected by further changes in CO₂ partial pressure. When only a partial protective film is present, an increase in CO₂ partial pressure may promote the formation of a more protective layer, thereby reducing the severity of localized corrosion and lowering pitting density.
As the number of oil and gas wells operating in CO₂/H₂S coexistence environments increases, the impact of H₂S partial pressure on corrosion has gained significant attention. Depending on its concentration, H₂S can affect the CO₂ corrosion process by altering the type and properties of the corrosion product film or by promoting anodic dissolution through sulfide adsorption. In the current standards for stress corrosion-resistant materials used in oilfield equipment, the H₂S partial pressure is typically restricted to 0.0003 MPa. Within this limit, the composition of the corrosion product film is primarily determined by the ratio of CO₂ to H₂S partial pressures, as well as temperature.
Dunlop et al. proposed that at room temperature, the corrosion product film is composed of carbonate when the CO₂ to H₂S partial pressure ratio exceeds 500, and of sulfide when the ratio falls below 500. Based on solubility calculations, the theoretical range for the CO₂ to H₂S partial pressure ratio that triggers the transition from FeCO₃ to FeS lies between 10²² and 10²⁴, as shown in Figure 20.
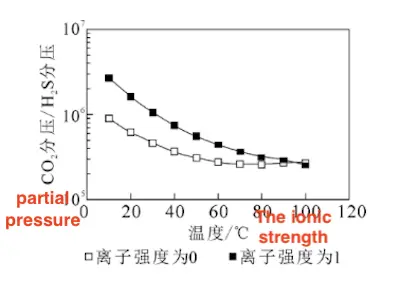
Figure 20 The theoretically calculated range of the CO₂ to H₂S partial pressure ratio for the transition from FeCO₃ to FeS under a CO₂ partial pressure of 0.1 MPa
The results indicate that as the H₂S partial pressure increases, the corrosion product film gradually shifts from FeCO₃ to FeS.
Some studies have suggested that small amounts of H₂S may help reduce the corrosion rate in a CO₂ environment. As previously discussed, in a CO₂/H₂S coexistence environment, H₂S can rapidly form a protective FeS₂ (Mackinawite) corrosion product film through a solid-state reaction, potentially lowering the CO₂ corrosion rate by an order of magnitude. However, other studies have reported that H₂S can accelerate CO₂ corrosion. Kvarekval et al. observed that despite the formation of a protective film on low carbon steel under conditions of 80 °C and pH 5.5–7.0, the corrosion rate still increased by a factor of 4–6. It is speculated that adsorbed sulfide and/or the sulfide film may enhance the corrosion rate through catalytic or galvanic effects. It is evident that the influence of H₂S partial pressure on the CO₂ corrosion process is not yet fully understood, making it a key focus for future research.
The influence of pH on the corrosion behavior of chromium-containing martensitic stainless steels remains a subject of debate. Sakamoto et al. reported that in a CO₂/H₂S mixed environment, a high pH increases the corrosion potential of modified 13Cr above the hydrogen evolution potential, leading to the formation of a stable in-situ passive film. However, as the pH decreases, the corrosion potential falls below the hydrogen evolution potential, promoting pitting corrosion and stress corrosion cracking (SCC).
Yao et al. reported that in a 5% NaCl solution without CO₂ and H₂S, the corrosion film formed on super 13Cr displays passivation behavior. As the pH of the solution decreases, the passivation behavior of the corrosion film improves, enhancing its protective function on the underlying metal. These findings suggest that pH primarily affects corrosion by influencing the passivation behavior of the surface film. However, the protective properties of the film are also influenced by factors such as alloy composition and temperature. For instance, super 13Cr alloyed with molybdenum (Mo) can form Mo-containing sulfides in the outer layer of the corrosion product film, significantly enhancing its protective performance and enabling the alloy to maintain corrosion resistance under low pH and elevated H₂S partial pressure conditions. Therefore, the effect of pH on the corrosion resistance of Cr-containing martensitic stainless steels warrants further investigation.
Chloride ions (Cl⁻) accelerate pitting corrosion by promoting the breakdown of the passive film on martensitic stainless steel in CO₂-rich environments. Li et al. reported that 13Cr stainless steel is highly susceptible to pitting corrosion at high Cl⁻ concentrations. As Cl⁻ concentration increases, both the breakdown potential and the repassivation potential of the passive film decrease. Autocatalytic reactions continuously generate iron cation and oxygen vacancies. Higher Cl⁻ concentrations cause these vacancies to accumulate within the passive film. When excess vacancies build up at the interface between the metal substrate and the corrosion product layer, partial detachment of the passive film occurs, leading to its failure.
Additionally, Cl⁻ indirectly influences the corrosion behavior of martensitic stainless steel by affecting the solubility of CO₂. Zhao et al. investigated the slow strain rate behavior of 13Cr stainless steel in NaCl solutions with varying Cl⁻ concentrations at 90 °C, under a CO₂ partial pressure of 3 MPa and an N₂ partial pressure of 6 MPa. They found that increasing Cl⁻ concentration decreases CO₂ solubility, thereby altering the cathodic reaction mechanism. At 5% NaCl, the sulfide stress cracking (SSC) mechanism in 13Cr is hydrogen-induced cracking, while at 20% NaCl, it shifts to anodic dissolution.
Molybdenum (Mo) contributes to the enhanced stability of the passive film under high-temperature and high-chloride conditions. Sunaba et al. reported that the addition of 2% Mo to modified 13Cr stainless steel facilitates the formation of molybdenum carbides, increases the effective chromium content, and improves the stability and repassivation ability of the passive film. These improvements significantly enhance the alloy’s resistance to pitting corrosion, as illustrated in Figure 21.
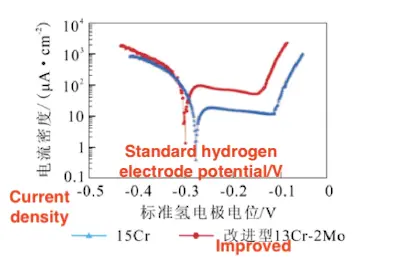
Figure 21: Potentiodynamic polarization curves of improved 13Cr-2Mo and 15Cr (Temperature: 180 °C, Cl⁻ concentration: 20,000 mg/L, CO₂ partial pressure: 4 MPa)
Research on the corrosion behavior of Cr-containing martensitic stainless steel in CO₂ environments has been ongoing for nearly 50 years, both domestically and internationally, leading to the development of a relatively systematic theoretical framework. However, the mechanisms by which environmental factors influence corrosion behavior remain a subject of debate. Research findings vary, particularly under complex conditions such as high temperatures, mixed gas environments, and elevated Cl⁻ concentrations—areas that require further investigation.
Future research and development can focus on the following aspects:
The Cr content can be optimized by refining alloy design, and predictive models for Cr content can be developed to suit various service environments. Additionally, alternatives to precious metals, such as Ni, should be explored to enhance economic viability without compromising material performance.
Most current CO₂ corrosion studies rely on post-analysis methods, with limited real-time in-situ monitoring techniques. Future research should focus on in-situ dynamic investigations of corrosion film formation, evolution, and breakdown to more effectively reveal the fundamental interactions between environmental factors and corrosion mechanisms.
Currently, there is no unified standard for CO₂ corrosion detection and acceptance. Corrosion behavior is influenced by multiple coupled factors—such as temperature, pH, Cl⁻ concentration, gas composition and partial pressure, and flow rate—resulting in inconsistent experimental outcomes. Therefore, it is crucial to develop a scientific and standardized corrosion evaluation system to support material selection, performance assessment, and the development of new alloys.
In summary, deepening our understanding of how environmental factors influence the corrosion behavior of Cr-containing martensitic stainless steels, along with advancements in in-situ techniques and standardization, will provide a stronger foundation for the reliable application of these materials in oil and gas exploration and production.